A Historic and Energy Intensive Industry
The cement industry, which is particularly energy-intensive and emits greenhouse gases, is subject to strict legal and environmental constraints.
However, the cement manufacturing process is complex and fuel and electricity requirements depend on many factors that complicate the energy optimization of the sites:
- Manufacturing method.
- Chemical composition.
- Quality (grain size in particular).
- Fuels.
- Quality of raw materials.
Do you want to optimize your energy performance? Digital solutions can help you:
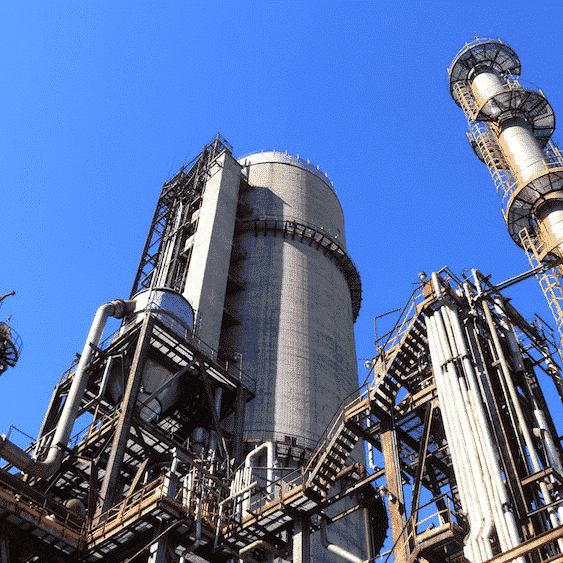
Energy-Consuming Equipment and Utilities in the Cement Industry
- Rotary kiln (inc. preheating and cold production).
- Grinders.
- Air compressors.
Digitalization for Optimal Energy Management in Cement Industry
Deploying a digital solution in your cement plant can help you reduce your energy consumption and your carbon impact while ensuring the sustainability of your know-how and production quality.
The METRON solution collects, stores and aggregates your internal data as well as external data such as weather and energy market prices in order to reduce your energy bill.
Benefits:
- A holistic view and customized dashboards.
- Control of cement product quality and energy consumption with defined KPIs.
- Malfunction reports and automatic alerts in case of deviations detection.
- Production forecasts based on energy prices.
Optimization actions can also be suggested to you, for example to reduce the electrical consumption of the mills or to optimize the energy mix and be part of a long-term energy performance approach.
Examples of Collected Data
-
Production: planning, type of product.
-
Energy consumption: all fluids.
-
Operational information: mill intensities, furnace temperatures, etc.
-
Regulatory constraints: smoke analysis: (NOx, Sox, etc.).
Case Study of a Brazilian Cement Industrial Group: Implement a Digital Solution to Save up to $78k in 1 Year
In this highly digitalized Brazilian cement plant, three mills are used to produce three types of cement, with a total production of 807,000 tons per year.
The cement plant wanted to meet a double objective: optimize the efficiency of the mills and plan their production according to market prices.
This has been achieved thanks to the deployment of our digitalized Energy Management & Optimization System. It has provided a holistic view of the plant, personalized dashboards by taking into account all the influencing factors to save time, reduce costs and improve collaboration.
The results? Estimated energy savings of 1,800 MWh per year for the three mills, which equates to a projected $78,000 reduction in annual electricity bills.
In addition to the gains from improved energy efficiency, the site is benefiting from a Demand Side Management solution, which also allows it to optimize its planning with respect to energy prices.