La digitalisation de l’énergie est au cœur de la transition numérique des industriels. Mais que recouvre-t-elle ? En quoi la transformation de données physiques en leviers digitaux actionnables permet d’avancer vers plus d'efficacité énergétique ?
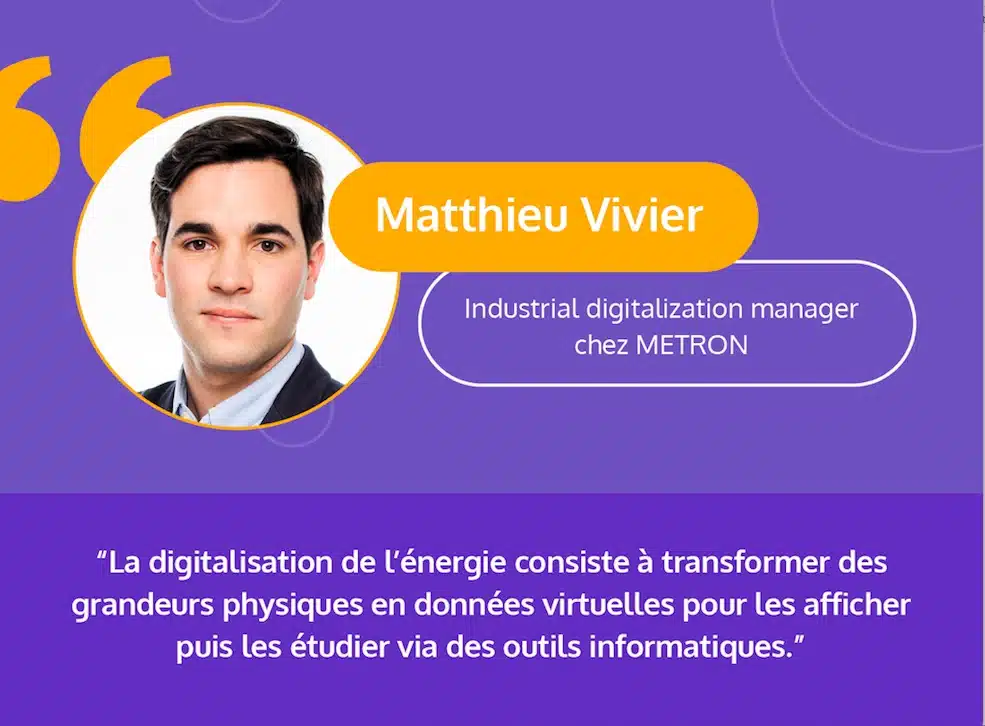
Matthieu Vivier dirige l'équipe internationale de digitalisation de METRON. Il présente le rôle de la digitalisation de l’énergie dans l’industrie, son périmètre et ses enjeux.
Comment définir la digitalisation de l’énergie dans l’industrie ?
Dans son acception la plus courante, la digitalisation est la transformation d’une grandeur physique en une donnée virtuelle qui peut être opérée sur un ordinateur.
Pour les sites industriels, digitaliser l’énergie, c’est donc :
- Collecter de manière sécurisée des données physiques énergétiques (températures, pression, vitesse, dimensions et contraintes du produit, etc.) sur les sites industriels mais également à travers des sources de données externes (prix de l’énergie, météo, etc.) ;
- Transformer des relevés physiques en données virtuelles qui peuvent être opérées sur un réseau ethernet, un ordinateur ou une machine ;
- Mettre à disposition des données pour être analysées par des ingénieurs énergéticiens, mais aussi par des experts en data science.
La digitalisation est le premier jalon indispensable dans la mise en place d'un energy management digital.
Pourquoi la digitalisation de l’énergie s'applique-t-elle à l’industrie ?
Contrairement aux systèmes bancaire ou médical, l’industrie n’a pas tout de suite pris le pli de la digitalisation, pour 2 raisons principales :
- dans les années 1980, l’énergie coûtait moins cher ;
- la grande complexité des procédés industriels, souvent uniques, ainsi que les contraintes techniques de collecte et de stockage des données limitaient son adoption.
Avec l'avènement du cloud, qui a permis la création de services tels que le machine learning et la data science, la digitalisation de l’énergie pour les industries a pris tout son sens : les données énergétiques sont alors devenues exploitables pour les industriels. Ces derniers se sont rendu compte du besoin de monitorer l'énergie avec des outils performants. Ils sont rapidement montés en maturité en installant des capteurs et des écrans de contrôle afin de récolter une multitude d’indicateurs physiques et de permettre que leur énergie soit analysée par des systèmes plus complexes, comme les clouds.
Par ailleurs, la transition énergétique est devenue une réalité – voire une priorité – pour les industriels, qui cherchent des solutions pour décarboner leurs émissions et réduire leurs coûts énergétiques. Ils peuvent désormais faire le choix de consommer moins ou de consommer mieux et au meilleur moment, grâce à l’analyse de données énergétiques et l’arbitrage des marchés de l’énergie déréglementés (comme en Amérique latine, mais aussi de plus en plus en Europe).
Cela participe non seulement à l’efficacité énergétique mais également à la performance industrielle, via l’optimisation des consommations de matières premières, le maintien de la qualité et la diminution des pertes et rebuts.
Sécurité, interopérabilité… Quels sont les enjeux de la digitalisation pour les industriels ?
Remonter les bonnes données
La digitalisation doit être pensée pour l’énergie. Un prestataire de digitalisation se doit d'avoir une connaissance approfondie du contexte afin de choisir les bonnes données et les informations qui ont de la valeur ajoutée, pour faire des analyses et obtenir de meilleures performances énergétiques, tout en évitant de remonter des données inutilement.
Une solution digitale agnostique, capable de collecter des données quels que soient les équipements, leurs fabricants ou les procédés dans lesquels ils sont utilisés, est un atout majeur. Cette grande flexibilité permet de chercher des données dans n’importe quel périmètre, de les corréler lors de la phase d’analyse et d’en tirer de la valeur ajoutée.
Le bénéfice est direct pour l’industriel : des insights, un monitoring en temps réel, des alertes pour réagir au plus tôt et minimiser les impacts des dérives, des outils de simulations pour anticiper les besoins énergétiques optimisés du site, etc.
Assurer la sécurité de ces données
Certaines pratiques bien connues comme l’espionnage industriel poussent les sites à se conformer aux plus hauts standards en matière de sécurité des données. Le danger se trouve à deux niveaux : le stockage (là où la donnée est accessible) et la transmission (lorsque la donnée sort du site ou arrive sur le cloud). Pour ne faire prendre aucun risque aux clients, on s’assure que les solutions respectent les politiques de sécurité de chaque site ou groupe industriel et soient compatibles avec les standards les plus courants et puissants du marché comme ceux d’AWS, Azure et OVH.
Ces méthodes sont différentes en fonction des groupes industriels. Pour assurer la compatibilité, il faut choisir une solution digitale qui ne s’enferme pas dans une méthode de sécurité et reste flexible pour répondre à un marché de la sécurité, des besoins et une demande qui, poussés par la recherche d’amélioration, évoluent constamment.
Bénéficier d’une grande puissance de calcul
La puissance et la capacité de calcul des clouds est nécessaire pour faire tourner des algorithmes d’intelligence artificielle et de Data Science. Elle permet aussi aux industriels d’opérer un grand nombre de données en temps réel et d'accéder à la plateforme de performance énergétique n’importe où dans le monde.
Un autre avantage majeur du cloud est qu’il permet aux clients de bénéficier d’une plateforme mise à jour en temps réel et qui dispose donc des fonctionnalités les plus récentes. Ce procédé est impossible à répliquer avec des serveurs en local, qui ne sont pas aussi performants que les serveurs d’un data center.
Chez METRON, quelles sont les spécificités de la digitalisation et comment s’opère-t-elle ?
La digitalisation correspond au suivi en temps réel de l’énergie chez les clients sur des outils informatiques. L’objectif est de faire de l’efficacité énergétique via l'analyse de données.
L’équipe digitalisation met en place la collecte des données sur les sites industriels et les envoie de manière sécurisée vers notre cloud. Notre but premier est de fiabiliser la collecte en créant un lien sécurisé avec les systèmes d’information de l’industriel. Nous sommes le premier lien entre la donnée récoltée et la donnée qui sera ensuite analysée.
Une solution compatible
La solution METRON peut s’interfacer aux systèmes existants. Elle peut, par exemple, extraire les données d’un EMS déjà implémenté ou d’un automate sur le réseau industriel.
C’est une vraie valeur ajoutée qui consolide l’existant et accroît la maturité des sites en permettant non seulement l’analyse en temps réel de sources de données diverses mais également l’analyse rétroactive d’un patrimoine de données.
Collecte de données : quelles sont les 2 méthodes possibles ?
Récupération des données directement chez le client
Les équipes METRON collectent la donnée chez le client à l’aide d’une machine virtuelle ou physique, qui fonctionne comme un serveur OPC et contient les drivers qui permettent de dialoguer avec tous types de protocoles industriels et envoient en temps réel et de manière sécurisée la donnée vers le cloud puis la plateforme. METRON propose aussi de récupérer les données directement via des liens cloud-to-cloud via des API standards si elles sont disponibles sur des clouds.
Envoi des données par le client
Les grands groupes industriels, qui ont déjà une infrastructure cloud, favorisent l' envoi de données via la connexion cloud-to-cloud. Le défi principal est alors l’interopérabilité. Il faut convertir les données dans un format qui correspond aux analyses et aux bases de données présentes dans le cloud METRON.
La diversité des systèmes d’informations industriels
Les informations physiques récoltées au sein des sites industriels sont hétérogènes. Les données peuvent en effet être issues de systèmes très différents :
- automates,
- supervisions,
- ERP,
- EMS,
- liaisons cloud-to-cloud et data lake (méthode de stockage de données massives utilisée par le big data),
- systèmes en place au niveau du groupe ou du site industriel.
Quelles sont les étapes de l’intervention de l’équipe digitalisation de METRON ?
Phase de cadrage du projet
Pour définir le cahier des charges technique et les schémas d’architecture réseau sécurisés permettant la récupération de données.
Phase de déploiement
Pour aider les équipes opérationnelles du site dans la mise en place du lien entre les systèmes internes et le cloud METRON.
Phase de support
Pour s’assurer du bon fonctionnement des flux de données, faire face aux déconnexions et mettre à jour la sécurité des systèmes d’information sur le site ou les protocoles d’envoi de données.
La force de METRON, ce sont des experts terrain qui connaissent les sites industriels, leurs procédés, leurs équipements, et les systèmes informatiques quelles que soient les zones de la planète.
L’équipe sait rapidement trouver des solutions pour centraliser en un même point les données de consommation d’énergie, les paramètres de procédés et les données de production nécessaires à chaque analyse énergétique.
Dans l’industrie, la digitalisation de l’énergie est une étape essentielle pour améliorer sa performance énergétique, puisqu’elle transforme les données collectées sur de multiples points d’un site industriel en données à forte valeur ajoutée à l’intérieur d’un système virtuel modélisé. Une fois digitalisées, les données contextualisées permettent d’établir des modèles de référence et de mettre en lumière les optimisations de performance grâce à l’expertise d’ingénieurs énergéticiens et de data scientists.
Vous voulez découvrir comment la digitalisation aide Danone à atteindre ses objectifs de développement durable ?
Le Global Performance Manager pour la nutrition spécialisée chez Danone nous a expliqué comment ils ont économisé jusqu'à 15% d'énergies grâce aux données existantes.