Per tutte le aziende che hanno optato per la transizione al digitale la digitalizzazione dell’energia è un aspetto di fondamentale importanza. Ma di che cosa si tratta esattamente? Qual è il ruolo della conversione dei dati fisici in spunti digitali azionabili ai fini del raggiungimento di una maggiore efficienza energetica?
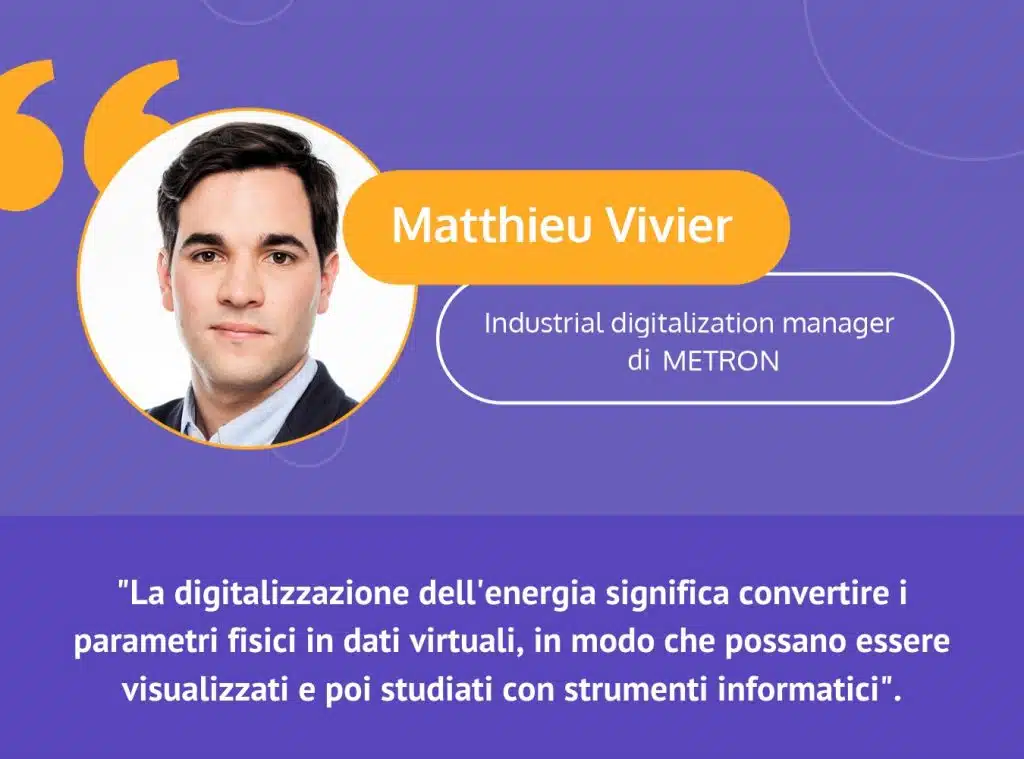
Matthieu Vivier è a capo del team internazionale di digitalizzazione di METRON. Qui parla del ruolo che la digitalizzazione dell'energia svolge nell'industria, delle sue finalità e delle sfide che deve affrontare.
Come si può definire la digitalizzazione dell’energia nell’industria?
Nell’accezione più comune, con digitalizzazione si intende la conversione di un parametro fisico in dati virtuali che possono essere elaborati al computer.
Per quanto riguarda gli stabilimenti industriali, digitalizzazione dell’energia significa:
- Raccolta in sicurezza di dati fisici sull’energia (temperatura, pressione, velocità, dimensioni e limiti imposti ai prodotti, etc.); non solo da sistemi industriali ma anche tramite fonti di dati esterne (prezzi dell’energia, informazioni meteo, etc.);
- Conversione di valori fisici in dati virtuali elaborabili su rete locale, computer o dispositivo;
- Messa a disposizione di dati per l’analisi da parte sia di tecnici dell’energia, sia di esperti in data science.
La digitalizzazione è il primo stadio dell’attuazione di un sistema di gestione digitale dell’energia.
Perché la digitalizzazione dell’energia è importante per l’industria?
Diversamente dai sistemi bancari o medicali, l’industria è stata relativamente lenta nel passaggio alla digitalizzazione, per due motivi principali:
- negli anni Ottanta del secolo scorso, l’energia era più economica;
- la grande complessità dei processi industriali (spesso unici) interessati e i vincoli tecnici per la raccolta e l’archiviazione dei dati ne hanno ostacolato l’adozione.
Con l’avvento del cloud, che ha reso possibile la realizzazione di servizi come l’apprendimento automatico e la data science, la digitalizzazione dell’energia per le industrie è diventata un concetto molto significativo: ora le aziende di produzione sono in grado di sfruttare i dati sull’energia. Esse hanno infatti capito la necessità di utilizzare strumenti potenti per il monitoraggio energetico. Sono così arrivate rapidamente alla maturità installando sensori e schermi di controllo per raccogliere una grande mole di indicatori fisici e consentire l’analisi dell’energia con sistemi più complessi, come i cloud.
Inoltre la transizione energetica è divenuta realtà - e addirittura una priorità - per gli imprenditori che sono alla ricerca di soluzioni per decarbonizzare le emissioni e ridurre i costi energetici. Ora hanno la possibilità di scegliere di consumare meno, o di consumare meglio e al momento giusto, utilizzando analisi dei dati energetici e l’arbitraggio dei mercati energetici deregolamentati (ad esempio, in America Latina, ma in misura sempre maggiore anche in Europa).
Ciò contribuisce a migliorare non solo l'efficienza energetica, ma anche il rendimento industriale, grazie ad un consumo più efficiente delle materie prime, a standard di qualità elevati e alla riduzione delle perdite e degli scarti.
Sicurezza e interoperabilità: quali sono le sfide della digitalizzazione che si trovano a dover affrontare le aziende di produzione?
Segnalazione dei dati giusti
La strategia di digitalizzazione deve essere ideata in funzione dell’energia. Il responsabile della digitalizzazione deve conoscere con precisione il quadro generale per poter scegliere i dati giusti e le informazioni a valore aggiunto, condurre analisi e ottenere un rendimento energetico ottimale, evitando allo stesso tempo di riferire dati inutili.
Un punto di forza primario è una soluzione digitale agnostica, che sia in grado di acquisire dati indipendentemente dai sistemi utilizzati, dalle marche degli stessi e dai processi in cui vengono impiegati. Questa grande flessibilità consente di cercare i dati in qualsiasi ambito e di correlarli durante la fase analitica, traendone valore aggiunto.
Ciò comporta un vantaggio diretto per le aziende: informazioni utili, monitoraggio in tempo reale, allarmi per consentire reazioni tempestive e ridurre al minimo gli effetti delle discrepanze, strumenti di simulazione per prevedere i requisiti energetici ottimizzati del sito, e via dicendo. I problemi vengono prontamente individuati, si agisce rapidamente e a fine anno si vede la differenza.
Messa in sicurezza dei dati
Alcune prassi consolidate - come lo spionaggio industriale - costringono le aziende ad adottare gli standard di sicurezza dei dati più elevati. Il pericolo esiste a due livelli: archivio (il punto di accesso ai dati) e trasmissione (il momento in cui i dati lasciano lo stabilimento o entrano nel cloud). Per garantire l’assenza di rischi nell’ottica del cliente vengono effettuati controlli finalizzati ad assicurare che le soluzioni siano conformi alle politiche di sicurezza per i singoli gruppi o stabilimenti industriali, e che siano compatibili con gli standard più comuni e più validi del mercato, come quelli prodotti da AWS, Azure e OVH.
Tali metodi variano da un gruppo industriale all’altro. Per garantire la compatibilità, è necessario scegliere una soluzione digitale che non sia legata ad uno specifico metodo di sicurezza e che rimanga flessibile, per poter soddisfare un mercato, dei requisiti e una domanda di sicurezza che cambiano continuamente a fronte della ricerca di migliorie.
Sfruttamento di una maggiore potenza di calcolo
Per eseguire algoritmi di intelligenza artificiale e data science servono la potenza e la capacità di calcolo tipici dei cloud. Ciò consente inoltre alle aziende di produzione di trattare grandi volumi di dati in tempo reale e di accedere alla piattaforma delle prestazioni energetiche da qualsiasi parte del mondo.
Un grosso vantaggio offerto dal cloud è quello di mettere a disposizione dei clienti una piattaforma che viene aggiornata in tempo reale e che, di conseguenza, presenta le caratteristiche più recenti. Si tratta di un processo non replicabile con i server locali, che non sono così potenti come quelli dei centri di elaborazione dati.
Quali sono le caratteristiche specifiche della digitalizzazione in METRON, e come funziona?
La digitalizzazione consiste nel monitoraggio in tempo reale dell'energia presso gli stabilimenti dei clienti con l’ausilio di strumenti elettronici. L'obiettivo è quello di conseguire l'efficienza energetica attraverso l'analisi dei dati.
Il gruppo che si occupa della digitalizzazione imposta il meccanismo di acquisizione dei dati presso gli stabilimenti industriali e invia i dati in modo sicuro al nostro cloud. Il nostro obiettivo primario è di consentire un'acquisizione affidabile tramite un collegamento sicuro con i sistemi informatici dell'azienda. Noi siamo il primo anello tra i dati che vengono raccolti e i dati che saranno poi analizzati.
Soluzione compatibile
La soluzione METRON è in grado di interfacciarsi con i sistemi esistenti. Ad esempio, può estrapolare i dati da un EMS già installato o da un PLC sulla rete aziendale.
Il risultato è un vero e proprio valore aggiunto, che consolida il sistema esistente e aumenta la maturità del sito, consentendo non solo l'analisi di fonti di dati diverse in tempo reale, ma anche l'analisi retroattiva degli asset di dati storici.
Raccolta dei dati: quali sono i due metodi possibili?
Ottenimento dei dati direttamente dal cliente
I responsabili di METRON acquisiscono i dati dal cliente tramite una macchina virtuale o fisica che funziona come un server OPC e contiene i driver necessari per comunicare con tutti i tipi di protocolli industriali e inviare i dati in modo sicuro e in tempo reale al cloud, e quindi alla piattaforma. METRON fornisce altresì un servizio di recupero dei dati direttamente tramite collegamenti cloud-to-cloud, utilizzando API standard, se disponibili per quei cloud.
Invio dei dati a cura del cliente
I grandi gruppi industriali, che già dispongono di un'infrastruttura cloud, preferiscono inviare i dati attraverso la connessione cloud-to-cloud. In questo caso la sfida principale è l’interoperabilità. I dati devono essere convertiti in un formato che corrisponda alle analisi e ai database presenti sul cloud METRON.
Diverse tipologie di sistemi informatici industriali
Le informazioni fisiche acquisite presso gli stabilimenti industriali sono disomogenee, in quanto i dati provengono da sistemi molto diversi:
- PLC,
- meccanismi di monitoraggio,
- ERP,
- EMS,
- collegamenti cloud-to-cloud e data lake (metodo di archiviazione di grandi quantità di dati utilizzato per i big data),
- sistemi installati a livello di gruppo o di stabilimento industriale.
Quali sono le fasi del coinvolgimento dei responsabili della digitalizzazione di METRON?
Fase di definizione del progetto
Definizione delle specifiche tecniche e degli schemi dell'architettura di rete sicura che consentiranno l'acquisizione dei dati.
Fase di realizzazione
Assistenza ai responsabili operativi sul posto per la realizzazione dei collegamenti tra i sistemi interni e il cloud METRON.
Fase di assistenza
Garanzia del corretto funzionamento dei flussi di dati, gestione dei problemi di connessione e aggiornamento dei protocolli di sicurezza dei sistemi informatici in loco o dei protocolli di trasmissione dei dati.
Il punto di forza di METRON sono i suoi esperti sul campo, che conoscono gli impianti industriali, i processi e le apparecchiature, e i sistemi informatici in ogni parte del mondo. Si tratta di persone che sanno come trovare soluzioni rapide in grado di realizzare una posizione centrale mettendo assieme i dati per il consumo energetico, i parametri di processo e i dati di produzione necessari per ogni analisi energetica.
A livello industriale, la digitalizzazione dell'energia è una fase essenziale per migliorare il rendimento energetico, in quanto converte i dati raccolti da più punti di un impianto industriale in dati ad alto valore aggiunto all'interno di un sistema virtuale modellato. Una volta digitalizzati, i dati contestualizzati consentono di stabilire modelli di riferimento e di evidenziare le aree di miglioramento delle prestazioni attraverso la competenza di ingegneri energetici e esperti nella scienza dei dati.
Vuoi vedere come la digitalizzazione può aiutarti a raggiungere i tuoi obiettivi di sostenibilità?
Il Global Performance Manager per la Nutrizione Specializzata di Danone ci ha raccontato come hanno risparmiato fino al 15% di energia utilizzando i dati esistenti.